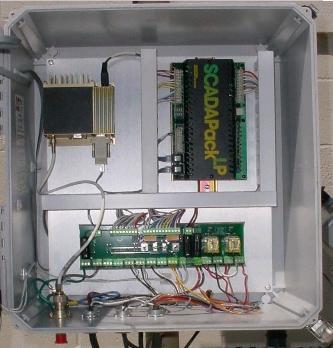

The Automation and Electronics, Inc. LP_FWCTM Flowing Well Production Controller is a marriage of the Control Micro Systems ScadaPackLPĀ® and our field proved flowing well controller firmware. The LP_FWC provides the operator with the latest in wellhead and gathering system pressure control. Solar powered units with radios provide local control with remote monitoring and control capabilities.
The LP_FWC provides the operator with options that allow for maximum fluid transfer without depletion of well bore pressure. Control functions can be configured by the operator to control on a single pressure parameter with pressure override or a combination of tubing pressure and gathering system pressure. Associated alarm and shut in set points are available on all analog input parameters.
Shutdown control functions can be configured to latch in until reset manually by the operator or to resume normal operation when the condition requiring the shut in returns to normal. Features such as this keep fluid production at its peak while still protecting the pressure limits imposed.
The operator can configure control parameters locally using an optional interface, PDA or portable computer. This allows the unit to be used in a stand-alone role without the requirement of a SCADA System. When used as part of a SCADA system, control parameters can be set remotely via the communication channel.
The standard unit includes the SCADAPack LP controller and the Automation Electronics SWIM Module. The SWIM module incorporates the valve actuator pulse and direction control relays, and local actuator control switches. Labeled field terminals for all analog input transmitters, and field status inputs are provided making installation quick and simple.
Features
General
- Wellhead and gathering system pressure control
- Manual valve override
- Local / Remote switch
- LEDs for easy status indication
- End element trend buffers
- Process input alarm and SD functions
Options
- Local operator interface
- RTU Link - handheld with rugged serial port & interface software
- 12 VDC @ 10 A battery backed supply
- 10 A-H/day solar power supply
- Wire line to wireless Ethernet
- AutoCom OPC connectivity
Software Modules
The LP_FWC application program is divided into the following modules:
- Elapsed time counter module
- LCD and key pad user interface module
- Time of day module
- Gauge off time module
- Field input scaling and alarm handler module
- ESD control module
- Control valve module
- Control valve override module
- ESD and run time totalizer module
- End element buffer module
Specifications
Mechanical | |
---|---|
Enclosure: | 18" x 16" x 10" NEMA 4X |
Environmental | |
---|---|
Operating temperature: | -40 to 158 deg. F (-40 to 70 deg. C) |
Relative humidity: | 5 to 90% non-condensing |
Power requirements | |
---|---|
Typical: | 12 VDC nominal @ 250 mA typical, less radio. |
CPU / Watchdog / Memory | |
---|---|
CPU: | 16-bit CMOS micro-controller and co-processor, 14.74 MHz clock |
Watchdog timer: | Integrated |
Memory: | 1 MB CMOS RAM, 513 kB flash ROM |
Input/Output | |
---|---|
Actuator I/O: | 8 each combination Input/Outputs (Valve open/ close status, computer/local control switch, open/ close manual override, valve open/ close control output relays) |
Analog inputs: | 6 each, 4-20 mA - (Header pressure, tubing pressure, casing pressure, optional temperature, differential pressure, optional flow, and battery voltage) |
Communication ports | |
---|---|
Operator interface: | 1 each RS-232 local |
Host data: | 1 each RS-232 Communications, licensed frequency, spread spectrum, and wireless Ethernet supported to 19,200 bps |
Local data: | 1 each RS-232 / RS-485 port |
Protocol: | AutoCom |