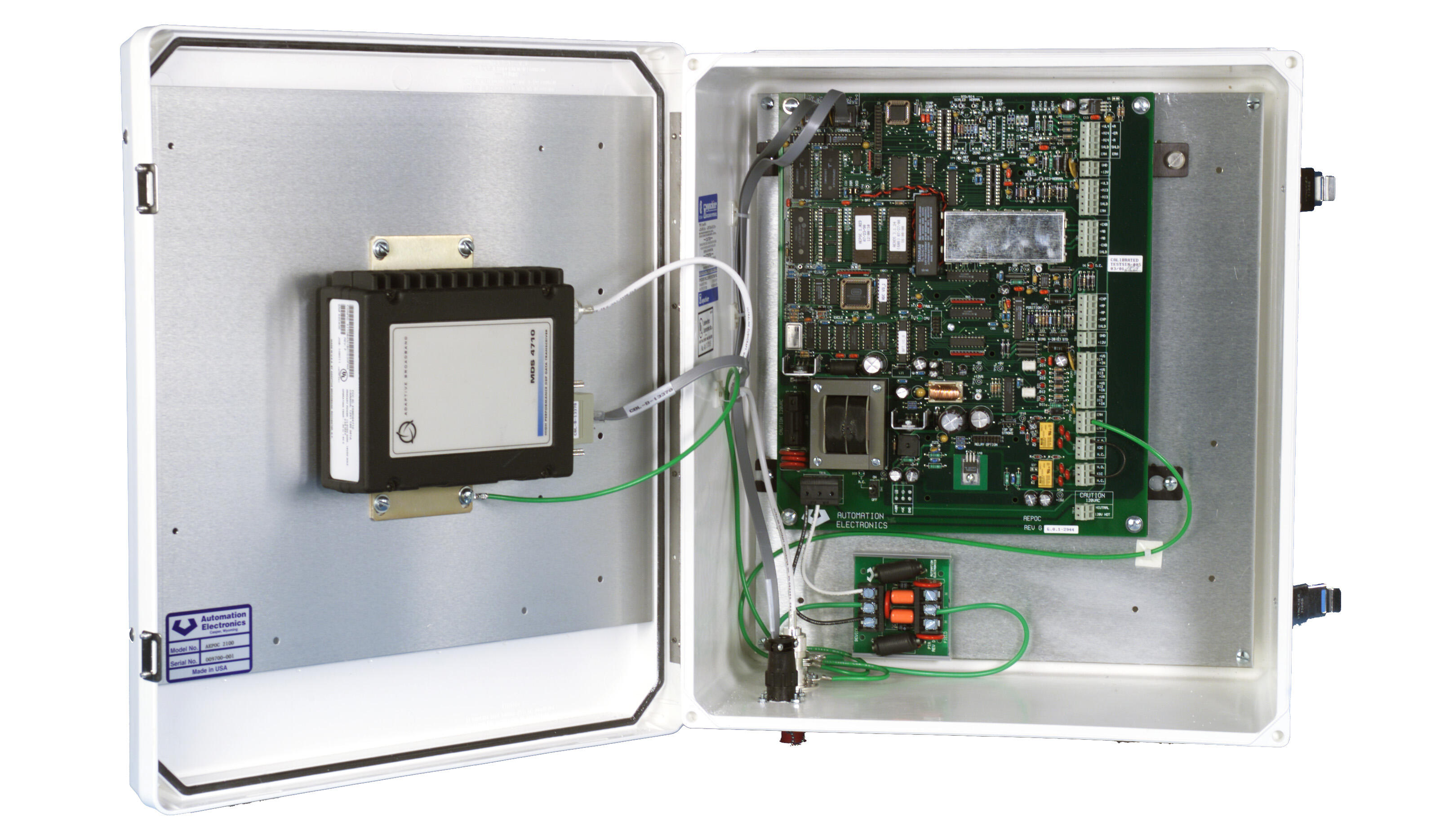
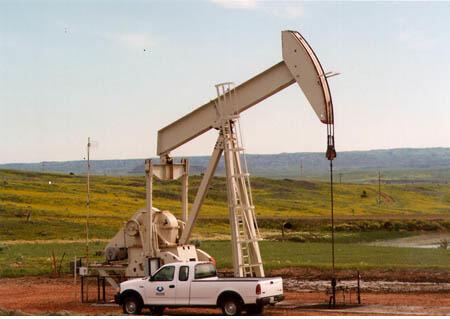
The AEPOC 2100 provides control for rod pumps and reports system conditions to a central host computer. Local rod pump control (RPC) software plus communications to a remote host computer helps protect assets and assure efficient reservoir management.
Running a pumping unit with a partially full chamber causes fluid pound that drastically reduces the useful life of the rod string, tubing, and pump. To minimize operating costs and extend the operating life of the unit, the AEPOC 2100 only allows pump operation if the well has sufficient fluid for efficient operation.
The AEPOC 2100 controls difficult wells at any depth. The flexible pump-off detection algorithm allows control of even horizontal or gassy wells. When the pump is only partially full (pumped off), the AEPOC 2100 stops the pump to allow well fluid to recharge. When used with variable speed drives the pump can be commanded to run at a slower speed while recharging to further increase production.
A wide range of alarms are available to limit damage from failures in the pumping equipment or rod string. The sensitivity and actions to take for these alarms is configurable. Input conditioning helps smooth out faulty data from end devices to keep your pump running.
Local data analysis and well optimization can be performed via laptop software or a rugged hand held data terminal. Communication with a centralized host computer allows remote optimization of pumping unit performance and allows field personnel to prioritize their work schedule using host computer alarms and reports, before going to field.
Accuracy
The AEPOC 2100 performs a highly accurate dynamometer card analysis with a wide variety of load and position sensors.
- A 16-bit analog to digital converter provides high-resolution load data from polished rod load cells or beam mounted strain gauges. The software conditions the data to remove load spikes.
- Proximity switches, potentiometers, damped and undamped inclinometers provide position information to the controller. A&Es RPC software fills in position information from a stored Base (Standard) Card between proximity switch closures. Well specific dynamometer Base Cards allow using rugged proximity switches for stroke synchronization while still receiving the benefits of continuous well analysis data. Improved tolerance for position potentiometers nearing their end of useful life and special compensation algorithms for inclinometers are embedded in AEPOC 2100 firmware.
- New improved surge and lightning protection (IEEE 472) protects load and AC inputs. An optional sacrificial ZAP-Stix board protects traces and allows plug-in field replacement.
Information Technology
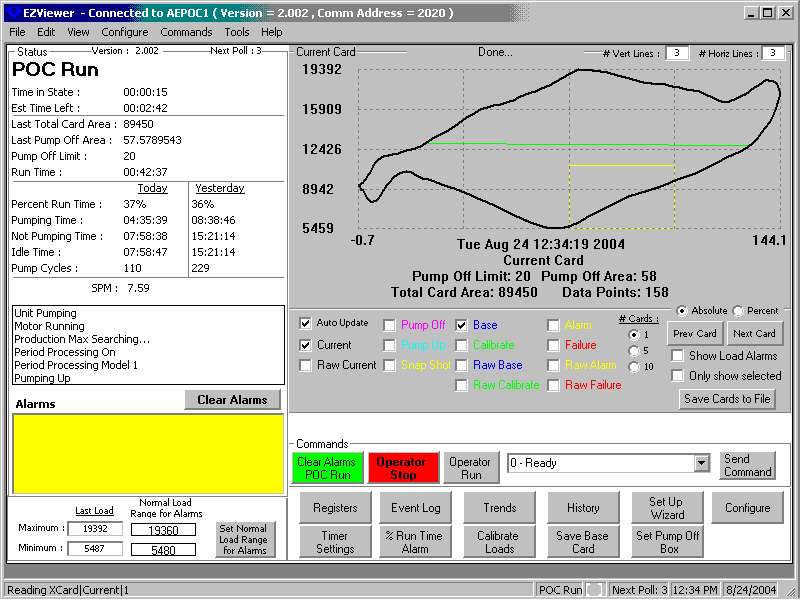
The AEPOC 2100 software provides friendly local user interface capabilities and remote host computer monitoring.
- The AEPOC EZ-Viewer...
- provides a high level interface to the AEPOC 2100, using dynamic buttons, pull down lists, and unit tagged fields for easy data display and configuration choice selections.
- organizes live and historical controller data and configuration information into functional easy to understand screens.
- provides templates to reduce individual well setup time and assure consistent AEPOC setup.
- provides upload and download capabilities to reduce technician time.
- runs on laptop PCs running Windows® 98, 2000, or XP.
- RPC alarm and status event processing...
- monitors symptoms of stress before failures occur.
- allows well analysts to fine-tune well performance.
- provides early detection when well chemical treatments and preventative maintenance is needed.
- helps lease operators, electricians, technicians, and well analysts prioritize their time.
- Historical data allows easy comparison of dynamometer cards for well-site or remote host trouble-shooting.
- Event logging helps determine root cause of pumping unit failures.
- If communication from the host computer fails, the AEPOC 2100 continues providing local intelligent control to ensure asset protection and maximum production.
Specifications
- Low cost
- -40 to +160 deg. F operating range
- 16 bit A/D load cell input
- On-board LED indicators on digital inputs and outputs.
- Flexible expansion capabilities with D/I and D/O daughter boards.
- 2 serial ports for local and host communication.
- RS-485 communications to optional wellhead controller and other dedicated cards for expansion I/O.
- MODBUS RTU, native AUTOCOM and Ethernet communication protocol support.
- OPC driver available for Human Machine Interface (HMI) & host computer systems.
- Graphic or alphanumeric HMI available in built-in or portable plug-in styles.
- Graphical EZ-Viewer PC based software provides easy customization and data analysis.
- Configurable standard alarms such as load and deep rod part alarms prevent hardware failures from causing more damage.
- Configurable responses to complex analysis of emulsion, paraffin and asphaltene problems allow maintenance to be scheduled before losing production.