The Automation & Electronics, Inc. ScadaPOC controls sucker rod pumps, minimizing operating costs while maintaining production.
The ScadaPOC’s main purpose is to be a sucker rod Pump-Off Controller (POC). A POC monitors the rod pump and detects when the pump chamber is not completely being filled so it can idle the pump and allow the well to recharge before resuming pumping. Continuously operating a pump with only a partially filled pump chamber wastes electricity, and can cause excessive wear and tear on the rod string, tubing, pump, and gearbox. This can greatly increase the costs of operating rod pumped wells.
Idling a pump until the well recharges significantly reduces excess equipment failures and their associated repair costs, down time, and lost production. Depending on the well depth, a ScadaPOC can pay for itself by saving just one rod string failure. This is how oil companies return the most value to the lease owners, partners and shareholders during the times when oil prices are high. This is also how companies can survive when oil prices fall.
Features
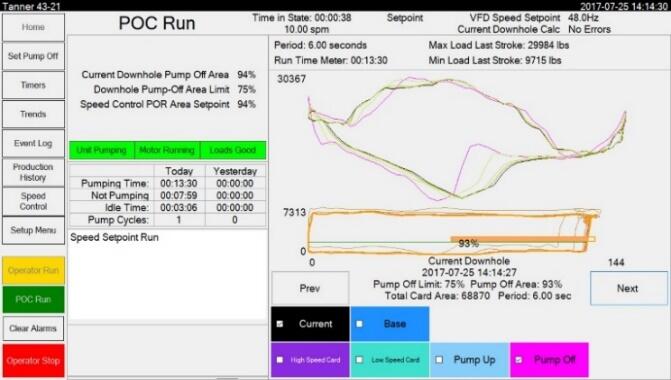
The ScadaPOC works by measuring polished rod load and position to generate dynamometer cards. These dynamometer cards are then processed in a flexible algorithm to determine when the pump is not being filled completely.
The ScadaPOC also has the capability to calculate downhole dynamometer cards, allowing it to display and control off of what is happening deep down at the pump.
Many types of equipment problems show up in the dynamometer cards along with the lack of pump fillage. The ScadaPOC has the diagnostic tools that analysts need to diagnose when problems occur. These diagnostic tools include event logging, tied to a history of alarm and failure cards, and configurable general purpose data trending.
Pumping Speed Control
The new ScadaPOC’s capabilities go beyond simply starting and stopping the pump. When paired with a Variable Frequency Drive, it can also regulate the pumping speed to match the well’s production rate.
Flexible Configuration
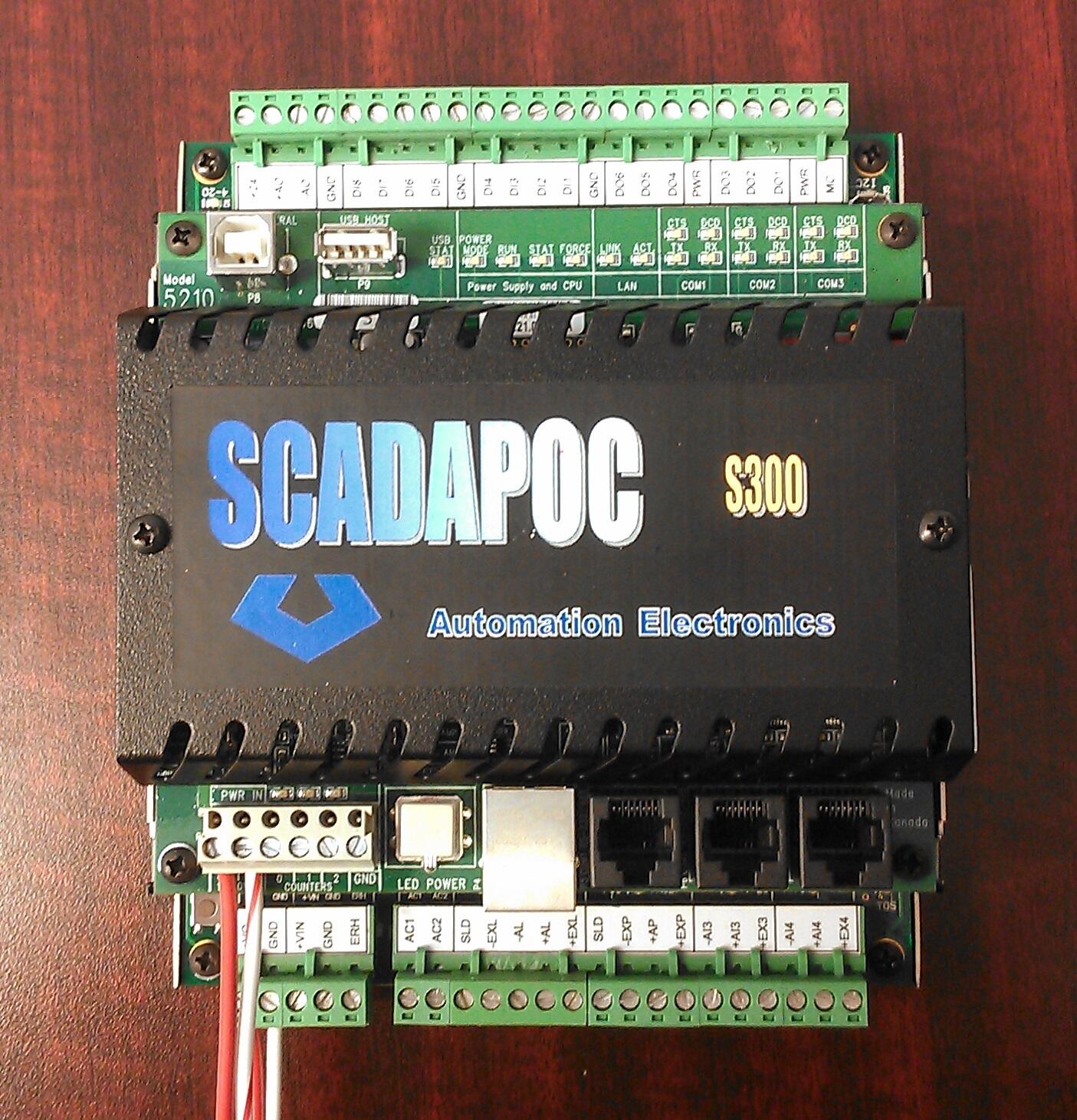
Not every field operation works in the same way. A one-size-fits-all POC solution doesn’t allow operators to change how their controllers work for them.
The ScadaPOC has the flexibility that allows users to customize their controllers to their fields. Instead of forcing users to use a specific type of load and position sensor, or one type of VFD, the ScadaPOC supports different types of sensors and VFDs.
Users can change many of the details of how their controllers work. The ScadaPOC also has user-configurable alarm and event handling. By learning how the one general-purpose structure is configured, a user can take control and tune the ScadaPOC to their operation’s methodology.
Ladder Logic Programming
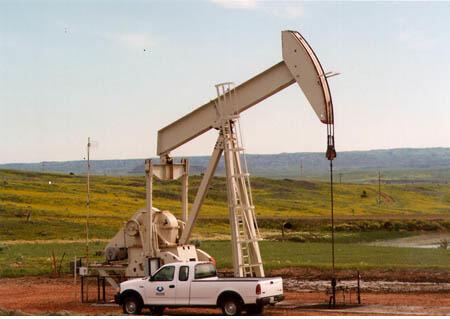
Users can add to the flexibility and controllability of the ScadaPOC as it now allows users to program additional features using standard ladder logic.
Operators can add additional I/O modules to the ScadaPOC to monitor and control other well site equipment with these ladder logic programs. Instead of adding separate controllers to suit their needs, users can expand their own ScadaPOC’s functionality.
SCADA Support
When used as part of a Supervisory Control and Data Acquisition (SCADA) system, operators can oversee their fields, know about problems quickly, and can gather accurate field data in all sorts of weather. This also gives oil field managers and engineers the tools they need to determine where to spend company resources. The ScadaPOC has flexible serial as well as Ethernet ports for different types of host communication networks.
Accurate and Reliable Load and Position Data for Consistent Operation
The ScadaPOC gets consistent and reliable information from a variety of load and position transducers. Use the type of load and position transducers you want. It's your choice.
- The ScadaPOC uses a 16-bit, wide dynamic range, differential voltage input for measuring loads from a variety of bridge type transducers
- An assortment of load cells are pre-programmed into the ScadaPOC. The parameters for new types of load cells can also be entered by the user.
- Beam mounted strain gauges are supported by the wide dynamic range of the load input as well as a proven compensation algorithm.
- The ScadaPOC uses a 16-bit analog input for measuring polished rod position from different position transducers including potentiometers, inclinometers, and switches.
- The ScadaPOC firmware compensates for drift, noise, and signal delay to handle various inclinometer types.
- For switches, the ScadaPOC can generate position information from different built-in pumping unit position profiles, or from a base stroke (where the position is established using a temporary potentiometer). The position switch can be mounted to trip anywhere within the stroke and the timing easily and accurately adjusted on the user interface.
Ruggedized Components for Oil Field Installations

Designed to comply with UL, NEC and NFPA requirements, the ScadaPOC can be sold separately or built in a UL 508A Listed control panel.
- NEMA 4 rated mild steel enclosure or polycarbonate NEMA 4X enclosure.
- Built from components that are designed and tested to operate in -40° C to 70° C (-40° F to 158° F) environments without the need for heaters or cooling fans.
- Capable of operating on 2 A @ 120 VAC power. The ScadaPOC can run off of the control power transformer in the motor starter.
- Fuses and terminals for wiring auxiliary well site systems.
- Cable ducting and terminal blocks for professional quality installations.
Graphical User Interface
EZViewer2 gives the user easy access to basic and advanced ScadaPOC functions and data displays.
- Runs on Windows XP through Windows 10 desktops, laptops and tablets.
- A setup wizard efficiently guides users through the steps of setting up their ScadaPOCs.
- Optional built-in display. To reduce installation costs and increase site security the HMI software can be run on a laptop or tablet.
- One HMI display can be used for all of the sucker rod pumps on a multi-well pad.
AutoCom and MODBUS Communication
The ScadaPOC communicates to a variety of host computer systems using the high performance AutoCom protocol.
- Optimized host communication performance for large data transfers including dynamometer cards.
- AEPOC compatible register translation for legacy host support.
- Configurable serial port to allow the ScadaPOC to use a wide variety of data radios and modems.
- TCP/IP Ethernet port is also available for network communications.
- Basic system status, operational commands and card data parameters are also available to MODBUS hosts.
Features and Specifications
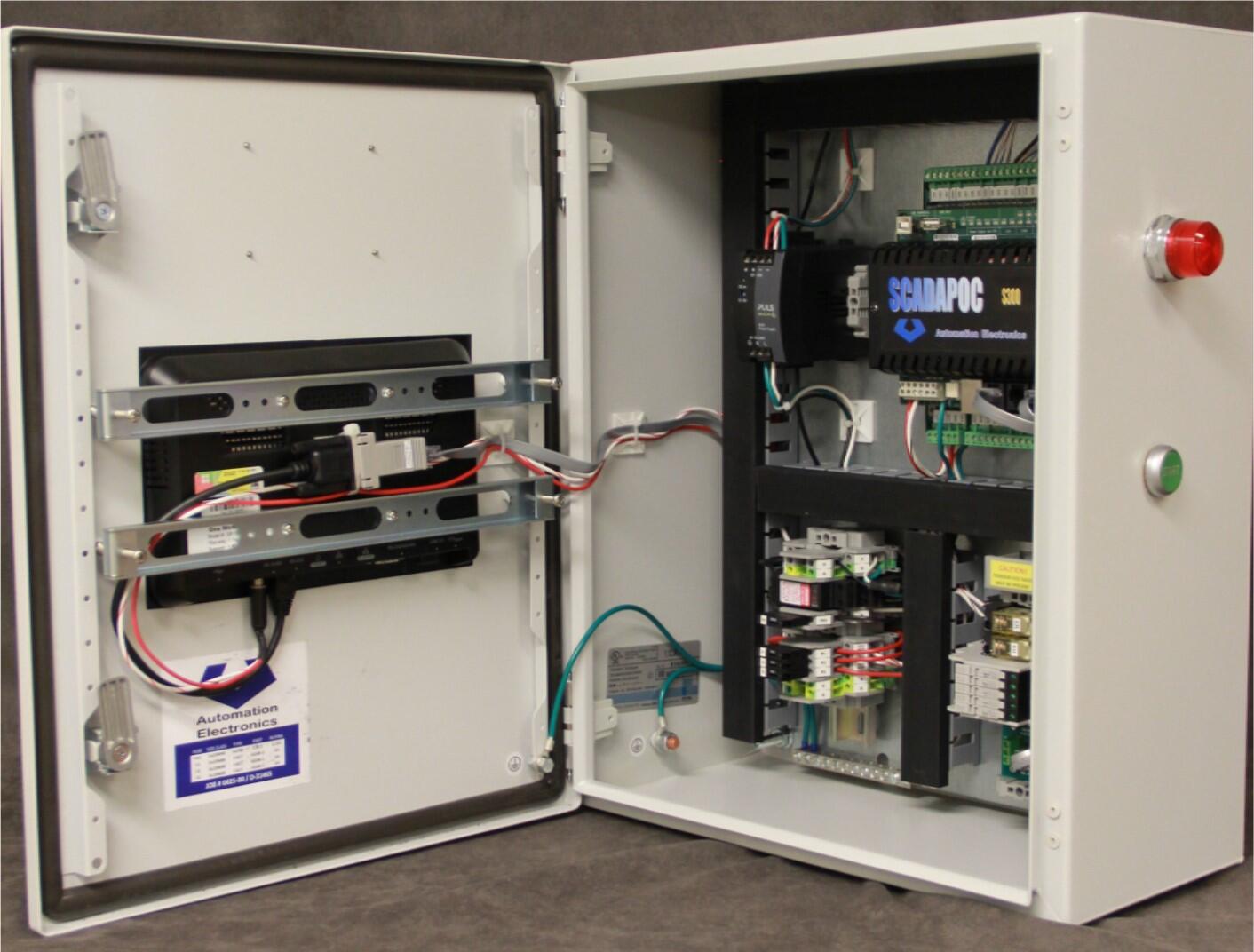
- Designed, built, and tested to work in extreme (-40° C to 70° C, -40° F to 158°F) oil field environments.
- 8 digital inputs
- 2 Hand/Off/Auto switch status, 1 Motor status, and 5 General purpose.
- Pull-down, internally supplied solid state digital inputs for immunity from stray induced voltages, and protection from short circuits without the need for fuses.
- 7 Digital outputs
- 1 Pump control and 6 General purpose.
- TTL with external Form C buffer relays provide for isolation and higher power outputs.
- Analog inputs
- 16-Bit 0 to 10 Volt position analog input to measure position.
- 16-Bit -150 to +150 mV differential analog input to measure loads.
- 2 16-Bit 4 to 20 mA auxiliary analog inputs.
- Analog output
- 1 16-Bit 4 to 20 mA auxiliary analog output.
- 16x20x8, NEMA 4, UL listed mild steel enclosure. (Polycarbonate, NEMA 4X and other size enclosures available on request.)
- 12 VDC, 60 Watt, UL listed NEC Class 2 power supply draws only 2 Amps at 120 VAC.
- 3 Amps at 12 VDC are available to power radio and other well site systems. (Higher power and 24 VDC power supplies are available on request.)
- UL listed circuit breaker provides protection from voltage surges.
- Built-in supply voltages for well transducers. Regulated 10 VDC supplied to load and position transducers, 24 VDC supplied to auxiliary analog inputs and output, 12 VDC supplied for digital outputs.
- Wiring duct for professional looking installations.